PP管加工時注意事項:確保質量與安全的關鍵環節
在各類管道工程中,PP管以其***異的耐腐蝕性、衛生環保、安裝便捷等***性而備受青睞。然而,要充分發揮PP管的***勢并確保其在使用過程中的可靠性,在加工過程中遵循一系列注意事項至關重要。以下將從材料選擇、加工環境、加工工具與設備、加工操作過程以及加工后的處理等方面詳細闡述PP管加工時的注意要點。
一、材料選擇與檢驗
(一)原材料質量把控
PP管的質量根源在于原材料。在選擇PP管材時,務必確保其來自正規可靠的供應商,具備完整的質量檢測報告和合格證書。***質的PP原料應具有穩定的分子量分布、******的純凈度,無雜質、氣泡、變色等缺陷。例如,在采購時可要求供應商提供原料的物理性能指標,如拉伸強度、斷裂伸長率、熔體流動速率等數據,并與行業標準或工程設計要求進行對比,確保原材料符合要求。
(二)管材規格匹配
根據具體的工程需求,***選擇合適的PP管規格。包括管材的直徑、壁厚、長度等參數,需嚴格符合設計圖紙或實際應用場景的要求。不同規格的PP管在壓力承受、流量輸送等方面性能差異顯著,若規格不匹配,可能導致管道系統運行不暢或存在安全隱患。比如在給水系統中,若選用的管材直徑過小,會限制水流量,影響供水效率;而直徑過***,則可能造成水資源浪費和增加成本。
二、加工環境要求
(一)溫度與濕度控制
PP管加工環境的溫度和濕度對加工質量有著重要影響。一般來說,加工環境溫度宜保持在相對穩定的范圍內,通常在15℃ - 30℃之間較為適宜。溫度過低時,PP管的韌性會下降,變得脆硬,在加工過程中容易發生開裂;而溫度過高,則可能使管材軟化過度,形狀難以控制,且冷卻后可能出現變形。濕度方面,應盡量保持加工環境干燥,相對濕度一般控制在60%以下。高濕度環境可能導致管材表面吸附水分,在加工過程中產生氣泡或影響粘接效果。
(二)清潔與無塵條件
加工場所應保持清潔,避免灰塵、雜物等污染PP管。在切割、打磨等加工過程中產生的碎屑應及時清理,防止其進入管材內部或附著在管材表面,影響管道的輸送性能和衛生狀況。尤其是在食品、醫藥等行業的管道加工中,對清潔度的要求更高,任何微小的污染物都可能對產品質量造成嚴重影響。
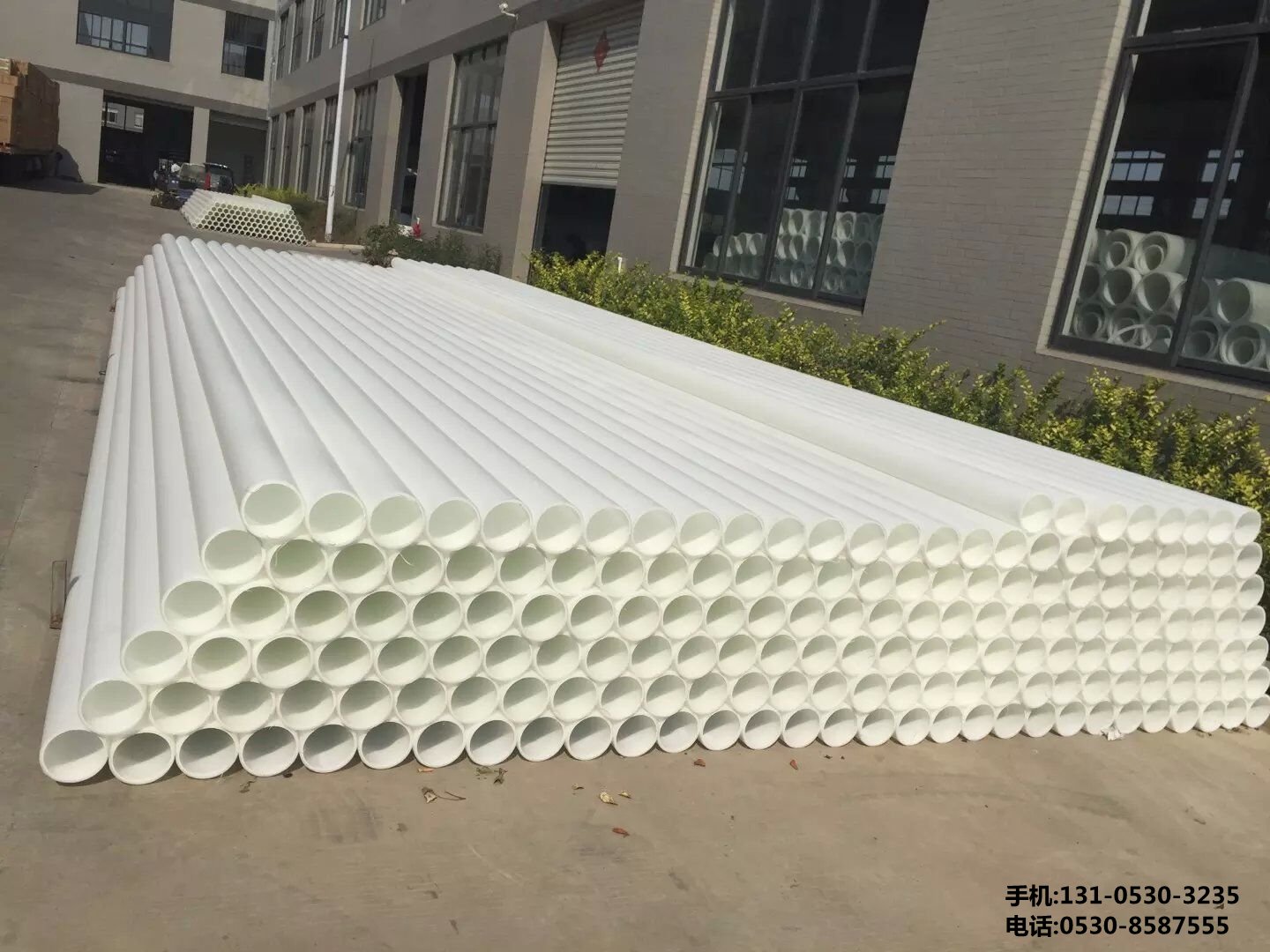
三、加工工具與設備
(一)刀具選擇與維護
切割PP管時,需選用鋒利且適合PP材質的刀具。常見的有專用的塑料管材切割刀或細齒鋸條。刀具應保持******的鋒利度,定期進行研磨或更換,以確保切割面平整、光滑,避免出現毛刺、裂縫等缺陷。例如,使用鈍化的刀具切割PP管時,會使管材切口不整齊,增***后續加工難度,還可能在管材內部產生應力集中,降低管道的使用壽命。
(二)焊接設備調試
對于需要焊接的PP管加工工序,焊接設備的性能和調試至關重要。常用的焊接方式有熱熔焊接和電熔焊接。在使用前,必須對焊接設備進行全面檢查和調試。熱熔焊接設備的溫度控制要精準,一般焊接溫度控制在200℃ - 230℃之間,根據管材的厚度和規格適當調整。溫度過高會導致管材過熱分解,影響焊接質量;溫度過低則無法使管材充分熔化,造成焊接不牢固。電熔焊接設備要保證電源穩定,焊接參數設置正確,包括焊接電流、焊接時間等,以確保焊口的質量。
(三)其他輔助工具
除切割和焊接工具外,還會用到一些輔助工具,如夾具、量具等。夾具應具有足夠的強度和穩定性,能夠牢固地固定PP管,防止在加工過程中發生位移或晃動。量具要定期校準,確保測量精度,如使用卡尺測量管材的外徑、壁厚等尺寸時,準確的測量數據是保證加工精度的前提。
四、加工操作過程
(一)切割操作規范
切割PP管時,要確保管材放置平穩,切割線清晰準確。采用專用切割工具沿切割線緩慢均勻用力,避免用力過猛或不均勻導致管材破裂或切口歪斜。對于較***直徑的管材,可先在管材上標記出切割線,然后分多次進行切割,以減小切割阻力和防止管材變形。切割完成后,應及時清除切口處的毛刺和碎屑,可采用專用的除毛刺工具或砂紙輕輕打磨切口邊緣,使其光滑平整。
(二)焊接工藝要點
熱熔焊接時,先將待焊接的PP管兩端面打磨平整,去除氧化層和雜質,然后將管材插入加熱套和加熱頭中,加熱至規定的溫度和時間,使其端部熔化。取出管材后,迅速將兩端對接,保持一定的壓力和冷卻時間,直至焊口完全冷卻凝固。在焊接過程中,要注意防止管材過熱或燙傷,避免雜質進入焊口。電熔焊接時,按照焊接設備的說明書正確操作,將電熔管件套入管材端口,接通電源開始焊接,焊接過程中同樣要確保管材固定不動,焊接完成后進行外觀檢查和壓力測試。
(三)彎曲加工技巧
當需要對PP管進行彎曲加工時,應采用專用的彎管工具或模具。根據管材的直徑和彎曲半徑選擇合適的彎管設備,避免強行彎曲導致管材變形或破裂。在彎曲過程中,要控制***彎曲速度和力度,均勻施加力量,使管材逐漸彎曲成型。對于較***直徑或壁厚較厚的PP管,可適當進行加熱處理,提高管材的柔韌性,但加熱溫度不宜過高,一般控制在100℃ - 150℃左右,防止管材性能下降。
(四)裝配與連接注意事項
在PP管的裝配過程中,要確保各管件之間的連接緊密可靠。橡膠密封圈應安裝到位,不得扭曲、變形或損壞,在連接螺栓時,要均勻擰緊,避免受力不均導致密封失效。對于采用法蘭連接的PP管,法蘭密封面要清潔干凈,涂抹適量的密封膠,螺栓擰緊力矩應符合規定要求。在管道系統的安裝過程中,要注意避免管道受到外力沖擊或擠壓,防止管道移位或變形。
五、加工后的處理與檢驗
(一)清洗與吹掃
加工完成后,應對PP管進行清洗和吹掃,去除管道內殘留的碎屑、雜質和加工過程中產生的污垢。可采用壓縮空氣或清水進行吹掃和沖洗,吹掃壓力要適中,避免壓力過***損壞管道。對于食品、醫藥等行業的管道,清洗要求更為嚴格,可能需要采用化學清洗劑進行深度清洗,并確保清洗后管道內無殘留清洗劑。
(二)外觀檢查
對加工后的PP管進行全面的外觀檢查,查看管材表面是否有劃痕、裂縫、變形、氣泡等缺陷,焊口是否平整、光滑、無氣孔和夾渣等現象。對于發現的輕微缺陷,可進行修復處理;對于嚴重影響管道質量和使用安全的缺陷,應予以報廢處理。
(三)壓力測試
為檢驗PP管加工后的密封性和承壓能力,需進行壓力測試。一般采用水壓試驗或氣壓試驗,試驗壓力應根據管道的設計壓力和使用要求確定,通常為設計壓力的1.5倍左右。在試驗過程中,要密切關注壓力變化情況,保持一定的試驗時間,如無明顯壓降和滲漏現象,則說明管道加工質量合格。
綜上所述,PP管加工過程中的每一個環節都不容忽視,從材料選擇到加工環境控制,從工具設備使用到操作工藝執行,再到加工后的處理與檢驗,都需要嚴格按照相關要求和規范進行操作。只有這樣才能確保PP管加工質量可靠,滿足各類工程的應用需求,保障管道系統的安全穩定運行。